# Follower PID Tuning
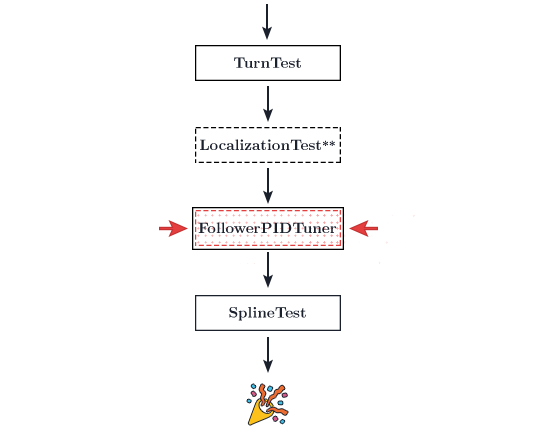
This is the last tuning step. Here, you will tune the closed loop feedback controller. This should improve your path following dramatically.
There are two alternative opmodes for this process, BackAndForth
or FollowerPIDTuner
.
It is recommended to run the BackAndForth
opmode to get a set of coarse PID gains and then run the same process using FollowerPIDTuner
for further fine tuning.
The BackAndForth
opmode simply travels in a straight line back and forth. It is easy to see major errors in translation and heading PID accumulate here.
The FollowerPIDTuner
will follow a large square. The bot will turn counterclockwise on each corner. If your heading is off, your entire square is destroyed and you have to keep resetting the bot. It's quite arduous. Use the BackAndForth
opmode for initial tunings and then continue to further fine tune with FollowerPIDTuner
.
Run the
BackAndForth
opmode via the RC.Then, connect to the RC phone's wifi network. The password to the network is located in the
Program and Manage
menu.Navigate to
192.168.49.1:8080/dash
with a phone RC or192.168.43.1:8080/dash
with a Control Hub.Ensure that you have the
Field
view selected in the top right.You should see two lines and two circles being drawn: green for the target position and blue for your bot's actual position.
Look for the
SampleMecanumDrive
in the right sidebar. Open that dropdown. You should be seeing two options:HEADING_PID
andTRANSLATION_PID
. Both options are located in theSampleMecanumDrive
file.Open up
HEADING_PID
first. Just keep increasingkP
until the robot starts to keep an accurate heading. This was around 8 in my experience, although your mileage may vary. You should not need to adjustkD
andkI
.Open up
TRANSLATION_PID
next. Once again, keep increasingkP
until the robot starts to adjust itself and follows the path. This was also around 8 in my experience, although your mileage may vary. You should not need to adjustkD
andkI
.Once that's tuned, you should be done! Remember that any changes in Dashboard must be reflected in the appropriate file. So, you should copy-paste your numbers into the PID object in
SampleMecanumDrive.java
.Feel free to run the same tuning process with
FollowerPIDTuner
. This is encouraged for further accuracy.You should be done! Go on to the
SplineTest
to ensure that your following is accurate.Note: Earlier I mentioned that you should not need to use
kI
orkD
for your follower PID's. Those are just basic guidelines.kD
actually indirectly functions as a P Controller on pose velocity. Therefore, settingkD
to a non-zero value (1 or something), IF you are using feedforward instead of velocity pid, may help keep your pose velocity constant across battery voltages. DO NOT setkD
if you are using drive velocity PID as they will overlap and fight each other.
# Informal Video
This was originally meant to be temporary, but was never finished, so the quality is atrocious but hopefully it ends up helping 😃, it should explain well enough.